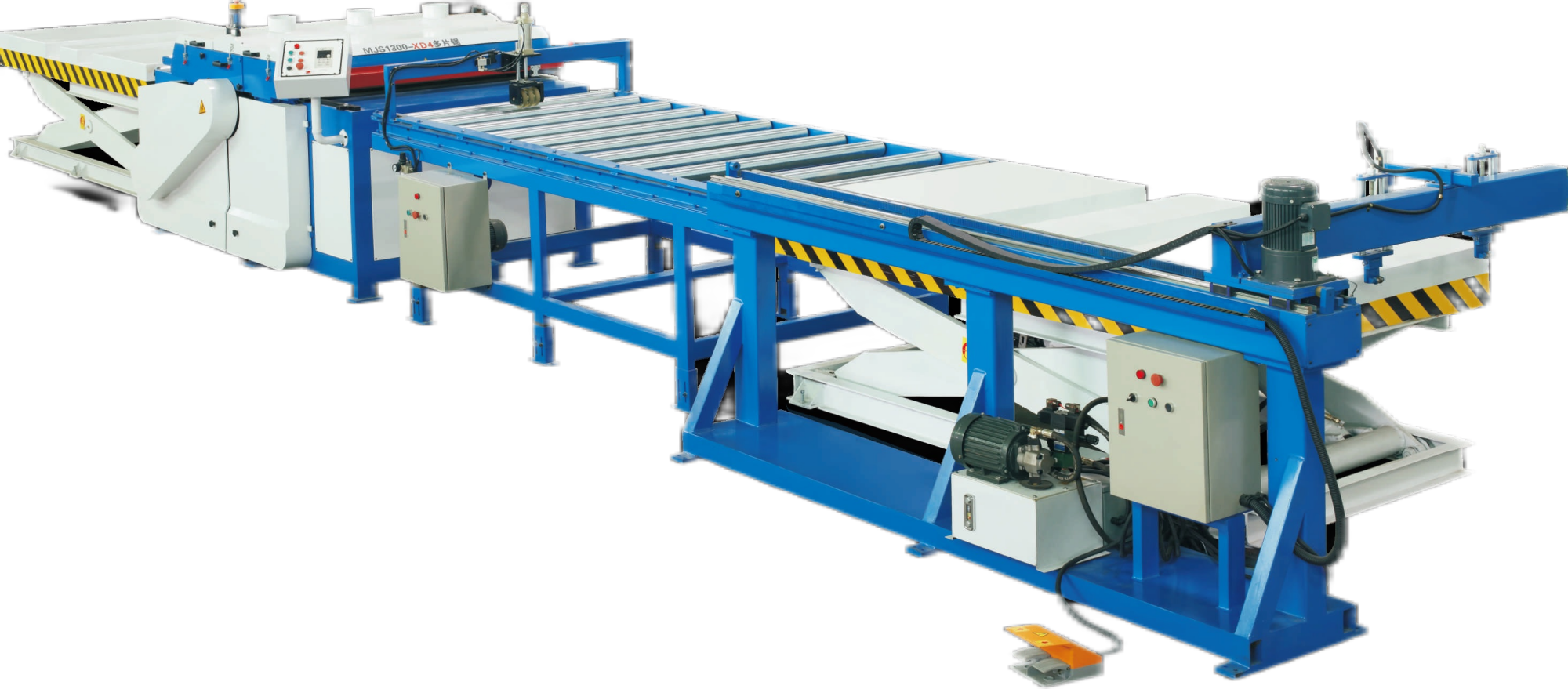
Maximize Productivity with HENGDA® Automatic Wood Panel Multi Blade Saw Production Line
In today’s competitive woodworking industry, automation is key to staying ahead. HENGDA®’s automatic wood panel multi blade saw production line leverages cutting-edge automation to streamline panel cutting for doors, furniture, and flooring manufacturers. By integrating fully automated loading/unloading systems, high-speed conveyors, and intelligent safety features, this production line dramatically increases throughput and reduces labor. Automation “streamlines the production process, reduces costs, and improves product quality“, helping wood processors achieve higher consistency and profitability.
Advanced Automation for Wood Panel Processing
HENGDA®’s solution is built on the proven HD1300 series of wood panel multi-blade rip saws – some of the most advanced machines available for panel cutting. These multi-blade saws are designed for continuous, high-volume production. The fully automatic system handles entire panels without manual intervention: material is automatically fed in, cut into precise widths, and then unloaded by conveyor. This eliminates tedious manual loading and minimizes downtime, delivering “increased efficiency and productivity”. Automated conveyors and handling systems boost throughput by reducing manual labor and minimizing errors or delays. In practice, this means manufacturers can cut more panels per shift with consistent accuracy – a clear advantage for large-scale woodworkers.
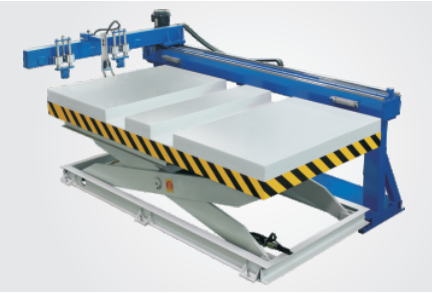
Fully Automatic Loading and Unloading Systems
At the heart of the line is a fully automatic loading/unloading system. Raw panels are placed on heavy-duty roller conveyor lines with specialized wear-resistant rollers. These roller lines (often made of high-strength, wear-resistant materials like nitinol rubber) grip each panel firmly. Once a panel is loaded, the system uses feeding scrapers and synchronized rollers to move it smoothly into the cutting zone. After sawing, photoelectric sensors detect the cut pieces and trigger automatic unloading onto exit conveyors. This seamless material flow means operators never need to manually handle heavy sheets, drastically cutting labor costs and improving workplace safety. Moreover, the automatic system can sort and align panels in real time, ensuring each board is cut to exact size with minimal waste.
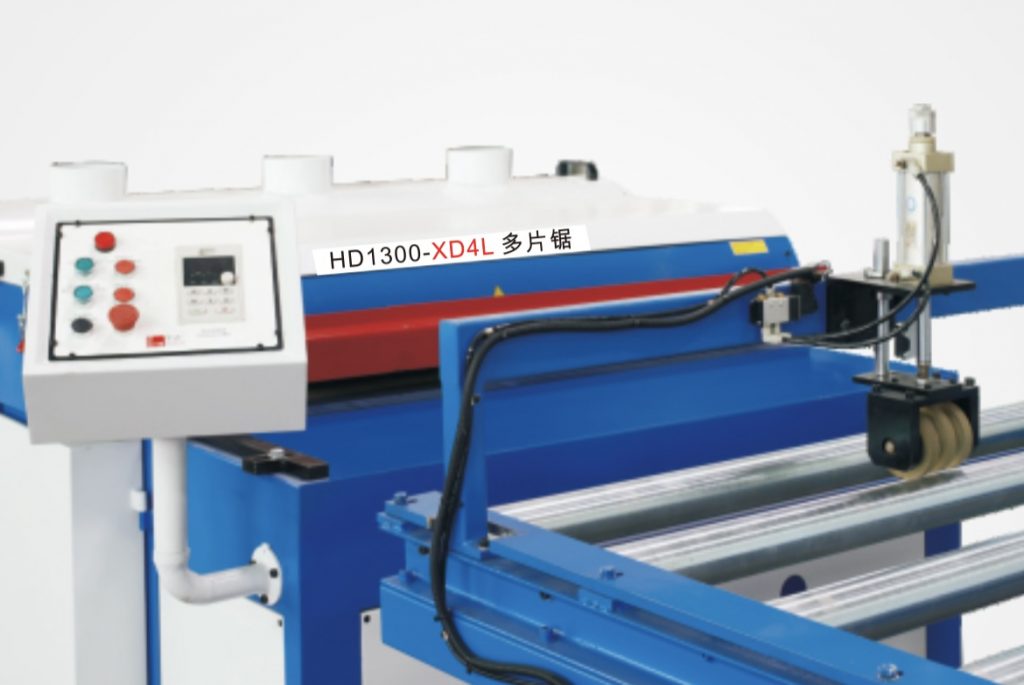
Enhanced Material Handling and Safety
Safety and reliability are built into every aspect of the line. HENGDA® machines feature sturdy steel frames that are stress-relieved and precision-machined for maximum stability. All saw units are enclosed with protective covers and interlocks: if a cover opens during operation, an automatic power cutoff immediately stops the blades, protecting operators. A dual anti-rebound protection system is also implemented – adjustable devices that grip panels at the top and bottom to prevent kickback during cutting. These features reflect that investing in automation “can also help to increase safety…reduce the potential for accidents and injuries”
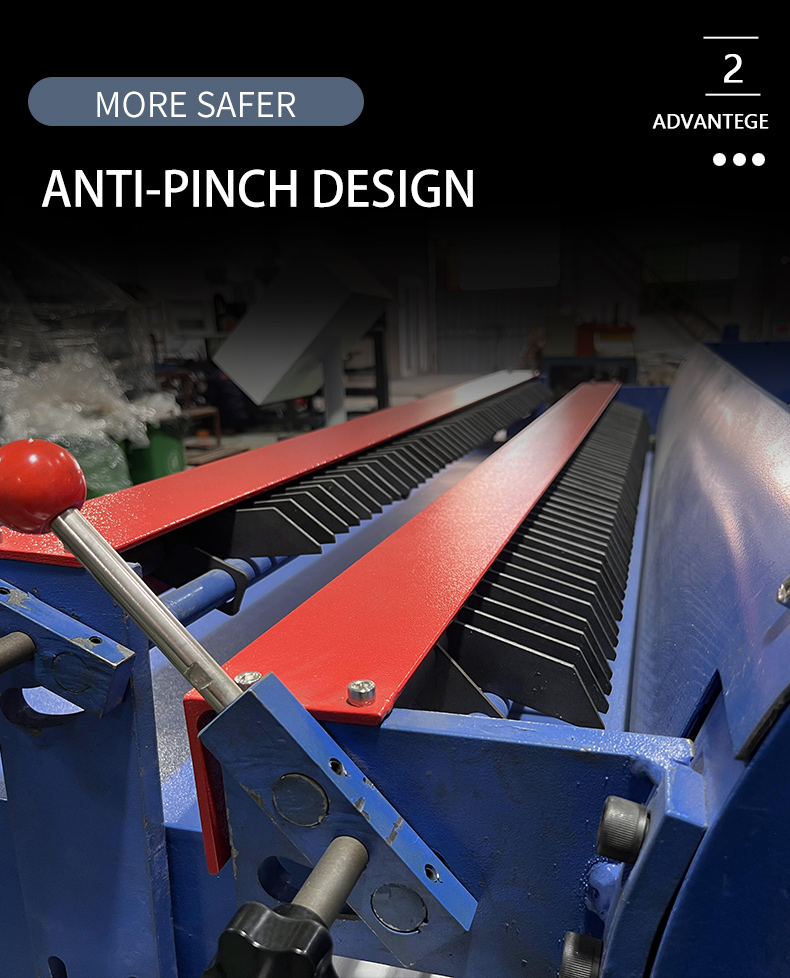
The material-handling components themselves are built for durability. For example, the feeding conveyors use multiple wear-resistant rollers in front and rear. One model boasts 14 nitinol-rubber rollers (eight front, six rear) with anti-slip surfaces, ensuring even very heavy or smooth panels feed without slippage. All rollers and chains are rated for heavy load and long service life. Even the spindle bearings are made from annealed ductile iron and dynamically balanced for minimal vibration. Together, these design choices give the line exceptional longevity, so manufacturers can run 24/7 with minimal maintenance.
High-Speed Output and Precision
Speed and precision go hand-in-hand on the HENGDA® line. The variable-frequency drive adjusts conveyor feed speeds up to 17 m/min, matching cutting rates to panel thickness and hardness. Cutting width capacity is 1220 mm (maximum 1260 mm), accommodating large standard boards. Despite the high speed, the system maintains tight tolerances (±0.2 mm on cut width) thanks to the precision-built frame and feeding mechanism. In practice, this means manufacturers achieve both high throughput and razor-sharp accuracy on every cut.
Multiple spindle configurations are available to suit production needs. Standard models use a single bottom-mounted spindle that cuts as panels pass overhead. An advanced dual-spindle model (HD1300-XT2L) adds a top blade for simultaneous cutting and slotting, ideal for two-in-one processing. Motor power options range widely (from about 11 kW up to 48 kW per spindle), so the line can be scaled from moderate to extreme-duty output. (With optional upgrades, some setups may reach as high as 55 kW per side.) In all cases, the rigidity of the machine frame and balanced spindles keep vibrations extremely low, maintaining smooth, burr-free edges even at high speed.
Flexible Configurations (HD1300 Series Compatibility)
One of the strongest selling points is the system’s flexibility. The HD1300 series encompasses several models (e.g. HD1300-X3L, XD3L, XD4L, XT2L) to fit different board thicknesses and production volumes. The production line can be configured to use the model that matches your throughput and board size requirements. For example, a small shop cutting thin panels might choose the 11 kW HD1300-X3L, while a large factory running heavy flooring boards would opt for the high-power HD1300-XD4L with multiple feeding rollers for maximum stability. Each setup uses the same automatic handling conveyor infrastructure, so integrating a new model is straightforward. This HD1300 compatibility means buyers can customize the line and even upgrade later as output needs grow, without redesigning the entire workflow.
Ideal for Doors, Furniture and Flooring Manufacturers
The benefits of automation are especially compelling for manufacturers of doors, furniture and wooden flooring. These industries require precision cutting of large panels at scale. By automating these cuts, companies cut back on manual labor and human error, thereby increasing yield. As industry analysts note, automation in wood processing delivers “higher quality products” with more consistent dimensions and higher throughput. In practical terms, a door factory using an automatic multi-blade saw line can feed in large MDF or solid wood boards and produce hundreds of identical door panels per hour. A flooring manufacturer can slice long planks or laminate sheets precisely and stack them via conveyor. Furniture part producers benefit similarly, ensuring each cabinet side or tabletop is cut uniformly. In all cases, the HENGDA® system’s high-speed automatic material handling dramatically improves productivity while reducing waste and labor costs
Technical Specifications (Example)
- Cutting Width: 1220 mm (max. 1260 mm)
- Feed Speed: 0–17 m/min (inverter-controlled)
- Motor Power: 11–55 kW (common models 11–48 kW each side)
- Panel Thickness: 5–60 mm (model-dependent)
- Feed Rollers: 6–8 sets, front and rear (wear-resistant, nitinol rubber)
- Machine Dimensions: ~2800×1800×1450 mm (varies by model)
- Safety: Full enclosure, auto shutoff on cover open; anti-rebound devices
These robust specs ensure that the line handles even the toughest workload. The powerful inverters allow precise control of feed rates, and the heavy-duty rollers and frame support long panels without sagging.
Conclusion & Call to Action
In summary, the HENGDA® Automatic Wood Panel Multi Blade Saw Production Line is a turnkey solution for wood processors aiming to maximize output and quality. Its fully automatic loading/unloading, intelligent material handling, and industry-leading safety features give manufacturers a competitive edge. Don’t let manual saws bottleneck your production – let HENGDA® provide a custom-designed automated cutting line. Contact HENGDA® today for a consultation and detailed production plan. Our team will tailor the HD1300 series line to your specific door, furniture, or flooring requirements, ensuring you achieve optimal throughput, efficiency, and ROI.