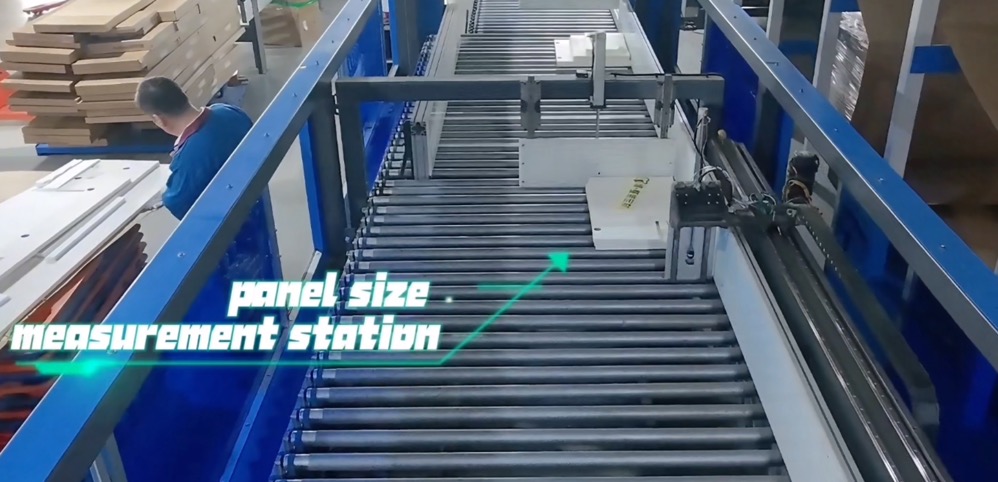
Hengda Intelligent Packaging Line With Seamless Dimensional Data Flow
In modern manufacturing, where extreme efficiency and perfect quality are pursued, every step of an intelligent packaging line must be tightly connected to achieve true automation. In Hengda’s intelligent packaging solutions, the measurement stations and intelligent corrugated carton cutting machines are not standalone units. Through seamless and efficient data flow, they work together to build the core of precise, efficient, and flexible packaging production.
The “Precision Sensing” of Measurement Station
As the first checkpoint in the intelligent packaging line, our measurement stations (such as MP-SJC, MP-SJCG, MP-SJCL) act as “sensors.” Their tasks include:
- Rapid Data Collection: When items to be packaged (such as panel furniture, stacked parcels, etc.) pass through the measurement station, whether using physical measurement or infrared light curtains, the station can quickly and accurately capture key dimensions like length, width, and thickness.
- For example, the MP-SJC achieves synchronous length/width measurement with an accuracy of ±1mm.
- The MP-SJCL, with its dual-station design and ±1mm accuracy, provides high-efficiency measurement.
- Real-Time Data Transmission: The high-precision dimensional data collected by the measurement station is instantly transmitted to the intelligent corrugated carton cutting machine via PLC in milliseconds. This process is fully automated, requiring no manual input or intervention.

The Cutting Machine’s “Customized Cutting”
Upon receiving precise data from the measurement station, our intelligent corrugated carton cutting machines (such as H6LD, H4A, etc.) immediately enter “intelligent response” mode:
- Instant Adjustment of Cutting Parameters: The cutting machine’s built-in intelligent software system (typically running on an industrial computer) calculates and automatically adjusts the cutting plan based on the transmitted dimensions. This includes:
- Determining the optimal unfolded carton size.
- Planning the most efficient cutting path (intelligent nesting).
- Adjusting the position and depth of creasing and slotting to perfectly match the current item’s dimensions.
- On-Demand Customized Production: Whether dealing with size variations between individual items or mixed batches of different specifications, the cutting machine can “instantly customize” perfectly fitting corrugated cartons based on real-time data. This “one item, one code; one package, one size” flexible production capability is unmatched by traditional fixed-mold production lines.
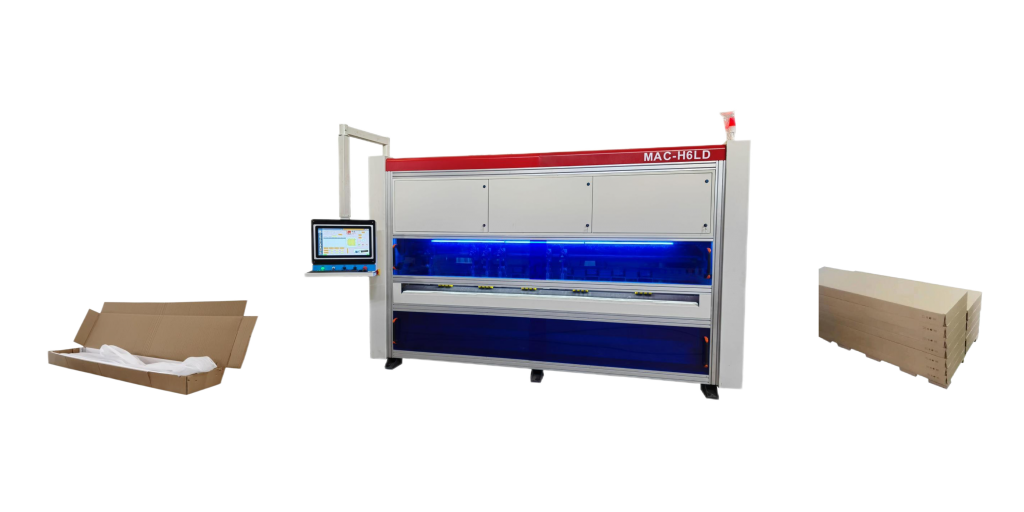
The Multiple Benefits of Seamless Integration
This data-driven collaboration between measurement stations and cutting machines brings revolutionary advantages to our intelligent packaging line:
- Eliminates Human Error and Efficiency Bottlenecks: Completely replaces the inefficiency of manual measurement, data entry, and parameter adjustments. The system automatically performs all calculations and adjustments, avoiding human mistakes and significantly improving overall efficiency and stability.
- Maximized Material Utilization: The measurement station’s precise data, combined with the cutting machine’s intelligent nesting algorithm, ensures every cut is accurate, minimizing waste and achieving approximately 25% material savings.
- Handles Complex Mixed Production: The production line can seamlessly switch between products of different sizes and shapes without downtime for mold changes or reconfiguration, greatly enhancing flexibility and adaptability—perfect for customized and diversified production needs.
- Ensures Packaging Quality: Since cartons are “tailor-made” to the product’s actual dimensions, they provide optimal protection, reducing movement and damage during transport. Additionally, precise cutting delivers clean edges and perfect box shapes, significantly improving the professional appearance and brand image of the packaging.
- Reduces Labor Costs: Automated and intelligent collaboration drastically reduces reliance on skilled operators and manual intervention, lowering long-term operational labor costs.
Building a Smarter, More Efficient Packaging Ecosystem
The core competitiveness of Hengda’s intelligent packaging line lies in the “flawless synchronization” between measurement stations and cutting machines. Together, they create a highly automated, data-driven intelligent packaging ecosystem that not only enhances production efficiency and cost-effectiveness but also delivers superior product protection through precision-customized packaging—helping businesses stand out in a competitive market. This deep integration of intelligent technology embodies the value that Hengda, as a “flexible packaging line expert,” is committed to delivering.
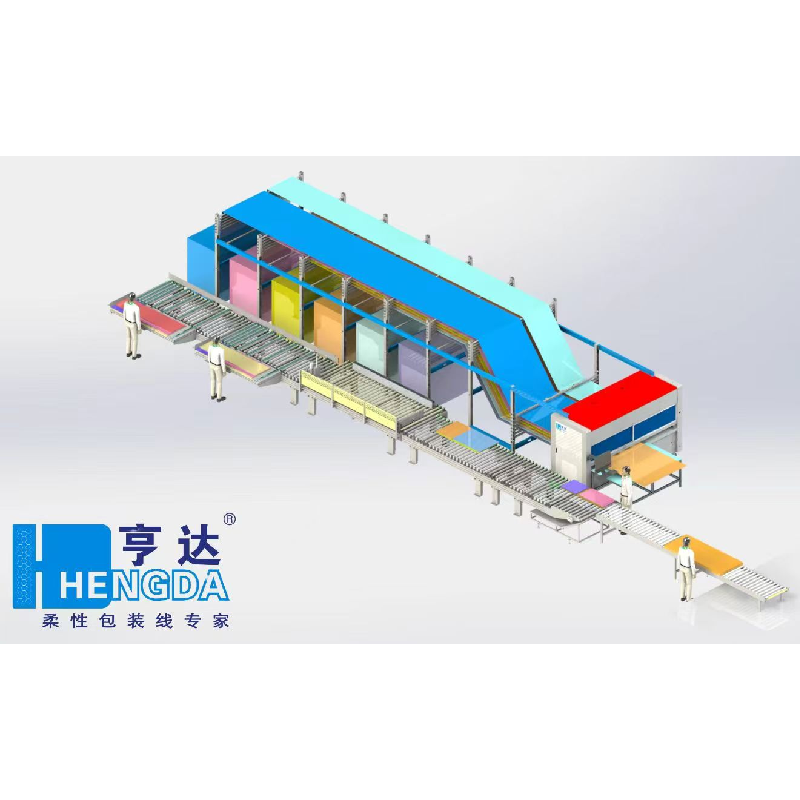