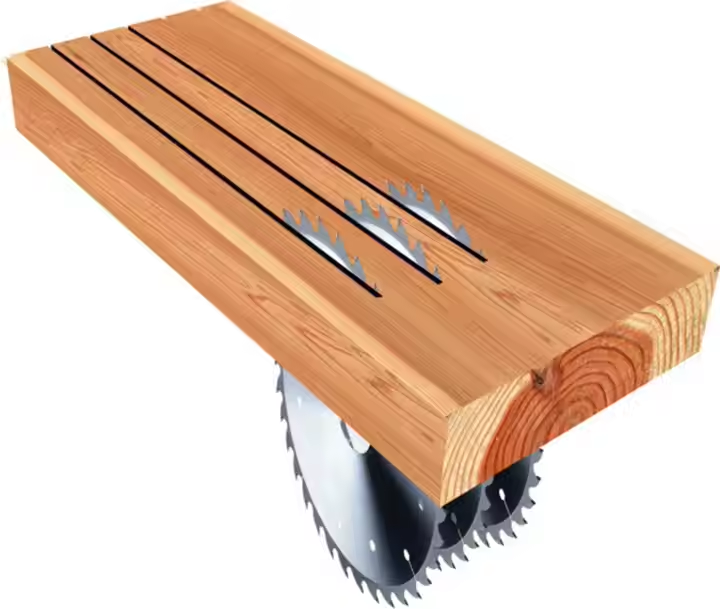
What to Look for When Buying a Wood Panel Multiple Blade Rip Saw Machine
Manufacturers cutting wood panels (MDF, plywood, particleboard, laminated board, etc.) often turn to a multiple-blade rip saw machine to speed production. Such machines feed a large panel through several circular saws on one arbor, slicing it into narrow strips in one pass. Multi-blade panel saws greatly boost throughput and part consistency – one maker notes that “adding a continuous-feed multi-blade rip saw production line increases your production rate and ensures the standardization and repeatability of your finished product”. When choosing a wood panel multiple blade rip saw machine, factory managers should evaluate capacity, feed design, cut precision, blade setup, maintenance, safety and energy features. Below are key factors, common pitfalls, and questions to ask suppliers before buying.
Panel Size and Material Compatibility
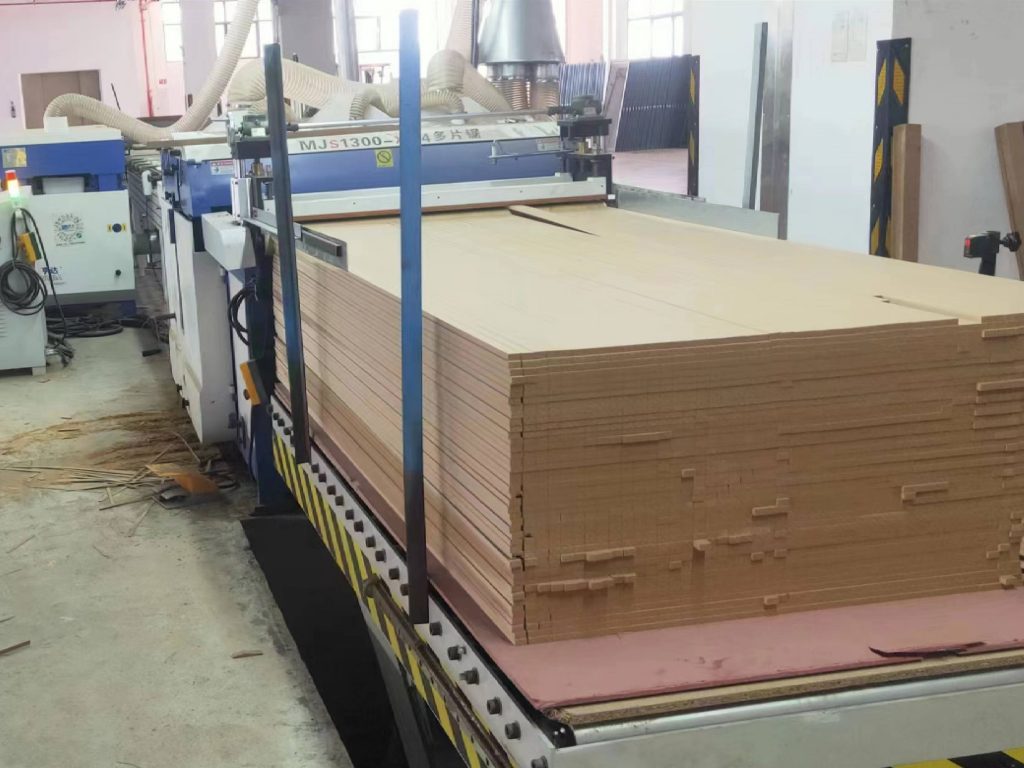
A critical first check is whether the saw machine can handle your panel dimensions and thickness. Standard sheet size in North America and many markets is ~1220×2440 mm (4×8 ft). Ensure the machine’s width capacity meets with your width demands. For example, one multi-rip model is specified for a 1220 mm max cut width, if your panel width is a little more than 1220mm, then it will depends on your cutting width demands, etc. Also confirm adequate length capacity or continuous-feed capability for long panels. Normally, there’s a minimum length for the panel as well. Panel thickness range matters too: many models handle 5–30 mm by default, and heavy-duty versions cut 10~40 mm or more (the Hengda HD1300-XD4L can rip up to 60 mm, and the HD1300-XD5L machine lists up to 30–90 mm. Choose a saw rated for the thickest materials you’ll process.
Material type is another concern. Ensure the saw’s blades and feed are suitable for MDF, plywood, particleboard, laminates, etc. Carbide-tipped, flat-top or alternate-top bevel blades are typically used for panel goods to avoid tearout. In summary: match the machine’s width, length, and thickness specs to your panel sizes, and verify it’s intended for wood‐based panels (not metal, for example). But nearly all kinds of wood can be processed by Hengda panel multi blade rip saw machine professionally.
Feed System and Material Handling
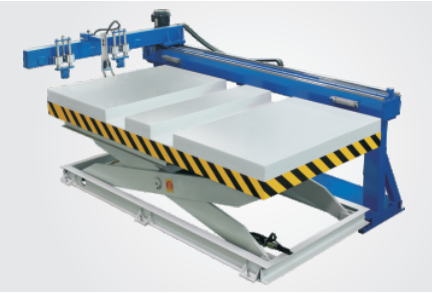
The standard feeding system including: hydraulic lifting table with panel pushing device, power roller conveyor. After the wood panel is pushed to the power roller conveyor, the powered roller conveyors feed panels into a continuous-feed multi-blade rip saw. In this example, an automatic panel feeder and driven rollers guide a plywood sheet into the saw
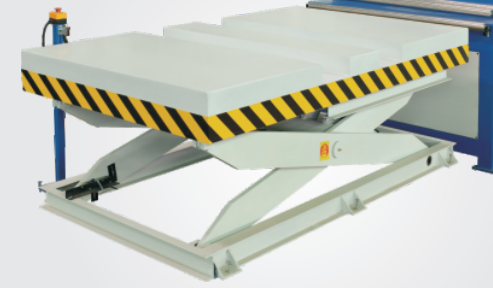
Also consider the infeed alignment and indexing. Hengda systems include a mechanical push-stop or pneumatic locator to square the sheet before cutting. Automatic feeders (e.g. vacuum tables or lift tables) can stage panels continuously. There’s also a alignment system for feeding to ensure the smooth material processing. Likewise, look at the outfeed handling. A stacker or scissor-lift conveyor under the saw can collect cut strips. For example, after cutting, the plank multi rip saw machine drops the strips onto a scissor-lift which lowers between each layer of strips. Ensure the saw can integrate with conveyors or lifters so that production is continuous and safe. Outfeed stacking system on a panel multi-blade saw. After slicing the sheet, the strips land on a scissor-lift conveyor that lowers between layers.
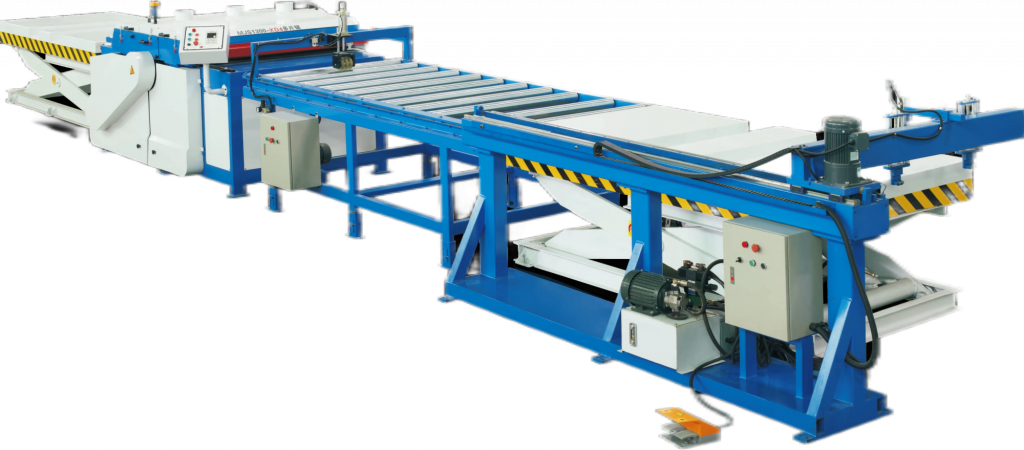
Blade Configuration and Cutting Precision
The blade arrangement determines how strips are laid out and how quickly you can change strip widths. In multi-rip saws, the blades stay on one long shaft and strips widths are set by spacers placed between the blades. Spacers give very consistent spacing and require minimal adjustment once set, which is good for high-repeat jobs. However, if you have several configurations for cutting, you should communicate with us to know what sizes of spacers you need in advance.
However, spacers changing when handle different cutting configurations is time-costing. Spacer changing for a full re-setup (re-spacing all blades) can be done in about 15–30 minutes normally(depending on the skillfulness of the operators). After upgrading the spindle of the saw machine by Hengda, the spacer changing time is shorten and more flexible.
However, some manufacturers would like to choose our advanced model—arbor change cart type enabling a complete blade-stack swap in a short time. You should communicate with us when purchasing, like how many cutting configurations? how automatic you want to achieve? what should I choose if I want to shorten the spacer changing time?
To ensure the cutting precision, like straightness, you’d better not change the standard blade default. Some customers want thinner blades to save cost, but we do not suggest because the blade default is set by our engineer after so many years of experience. Our standard blade default must be the most cost-efficient to achieve the best effect.
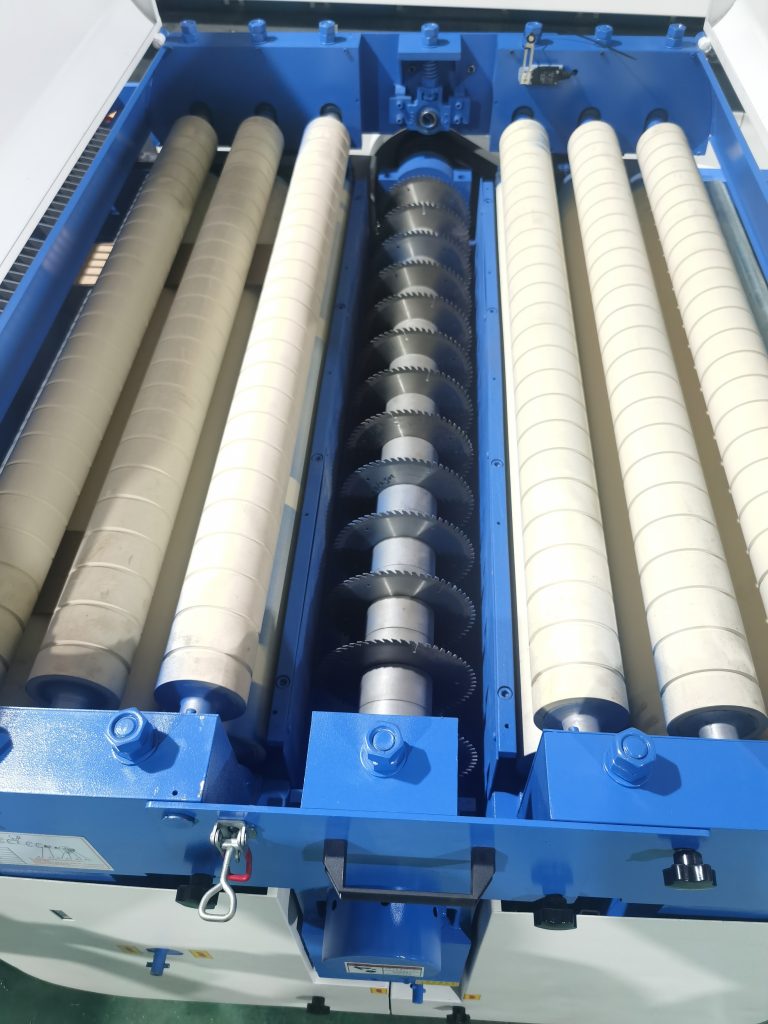
Safety and Dust Control
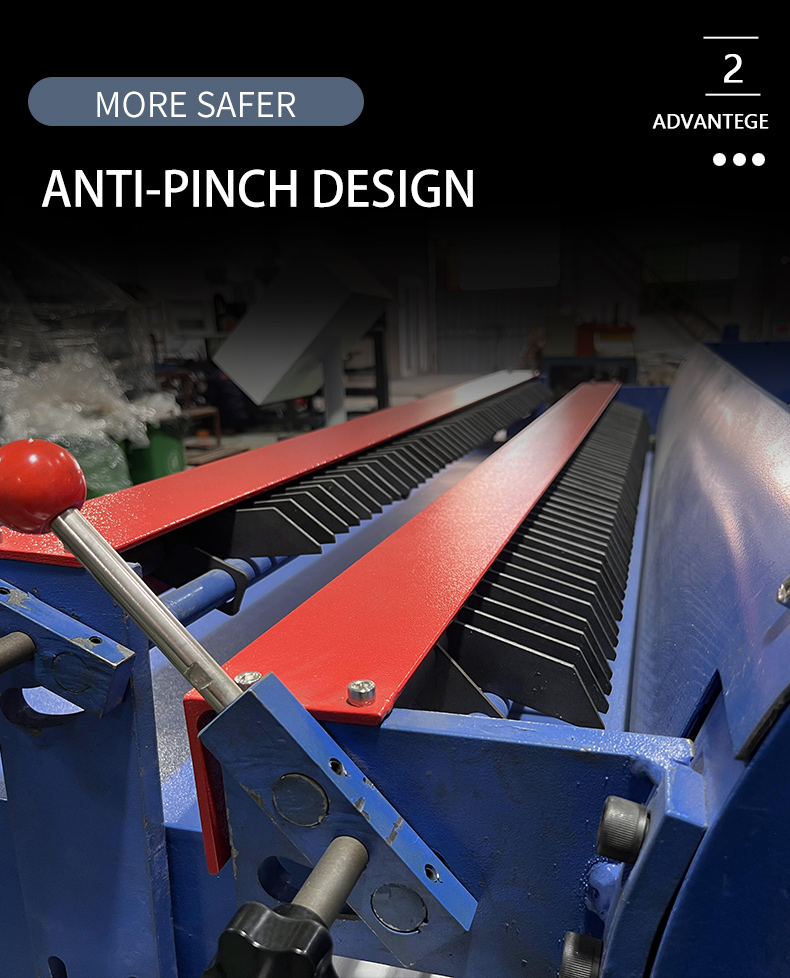
Cutting with multiple high-speed blades poses serious hazards. Ensure the saw machine has robust safety features. At minimum, look for anti-kickback devices: Hengda plank multi-rip saws include sets of spring-loaded fingers and press rollers to prevent boards from being thrown back. Hengda’s saw machine is equipped with “multiple sets of anti-kickback fingers, hold-down rollers, and side protection guards” on each blade. Solid hold-down or pressure rollers over the panel are also safety devices, reducing the chance of a board lifting or jumping. The saw should have clearly labeled emergency-stop buttons within easy reach on both sides. Also, there’re emergency stop front and back of the machine.
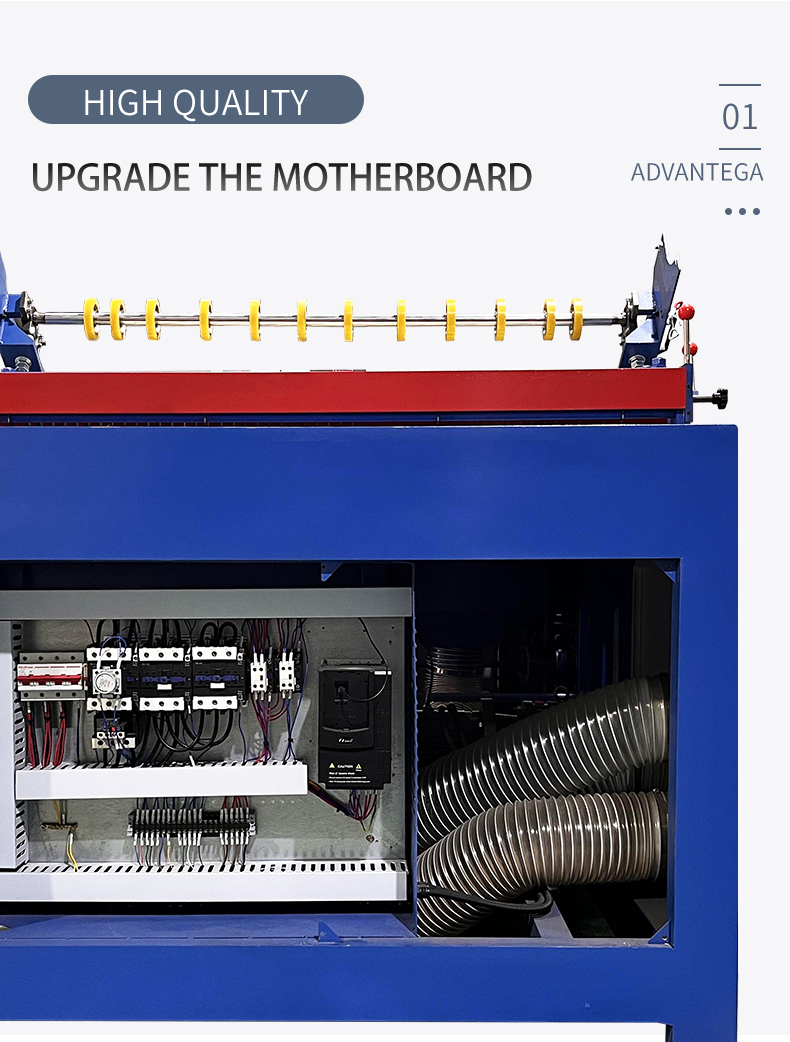
Dust extraction is both a safety and health issue. Wood dust from ripping panels can be large-volume. Good machines provide sizable ports for a dust collector. For instance, Hengda machine specifies a 1000 CFM dust collector with two 6″ ports. This reflects typical requirements – be prepared to hook up an industrial vacuum capable of handling the chip flow. If your shop has a central dust system, confirm compatibility (hose diameters and airflow).
Other considerations: noise and guards. These saws are loud, so hearing protection is mandatory. Some models may offer quiet zones or insulated covers for the motor. The upgraded machine from Hengda let the noise volume be minimum now. All rotating parts should be enclosed where possible. Finally, floor space and emergency egress should be planned: multi-blade saws often require clearance around the feed and exit sides for long panels.
In summary, safety means: anti-kickback features, hold-downs, side guards, emergency stops, and adequate dust collection. Never buy a used saw unless all guards and safety interlocks are present and in good condition.
Common Pitfalls to Avoid
- Ignoring actual capacity. Don’t assume “continuous feed” handles all panels – confirm the real cutting width, length, and thickness range.
- Overlooking feed grip. A powerful motor is useless without traction. Beware of slip: cheap machines may have insufficient or unadjustable hold-down rollers.
- Neglecting dust management. A saw that looks great on paper can choke if you have inadequate dust extraction. Underpowered extraction leads to jammed rollers and health hazards.
- Undersizing the motor. If you need frequent deep cuts in hard material, a small motor will bog down and burnout.
- Poor blade configuration planning. Failing to plan blade spacing sets or ordering the wrong spacing parts can shut down production. Make sure you get enough spacers or collars for all your jobs.
- Low-balling the budget. Very cheap saws often cut corners on rigidity, electronics, or drive components. It’s better to pay more upfront than lose production to downtime.
Questions to Ask the Supplier
- Capacity: Can your machine handle these panel width, length, and thickness?
- Blade Details: How many blades on the arbor by default? What are the blade diameter, thickness, and arbor size? Do you supply a starter set of blades, spacers or collars?
- Adjustment Time: How long does it take to change blade spacing or swap out blades? Are arbor stands or carts included or optional?
- Table and Support: How large is the outfeed table? Is there extension support for long panels?
- Safety: What safety features are standard (kickback fingers, guards, emergency stops)? What dust ports are provided and what extraction CFM is needed?
- Controls: Is there an electronic control panel? What diagnostics or error displays does it have? Does it accept automation or PLC integration?
- Power Requirements: What are the electrical requirements (voltage, phase, amps)? Does it include energy-saving drives or modes?
- Customization: Can the saw be fitted with optional equipment like automatic feeders, stackers, or workpiece supports?
- Price and Delivery: What is the base price, and what drives it higher (options, blades)? What is lead time for delivery and installation?
Asking these questions and cross-checking specifications will help ensure you choose a multi-blade rip saw that truly fits your manufacturing needs.
Conclusion
A wood panel multiple blade rip saw machine can transform panel processing by slicing boards into precise strips at high speed. To get the right machine, scrutinize its capacity, feed mechanism, blade setup, and safety features. Evaluate build quality for cutting accuracy, and ensure easy maintenance access (blade changes, lubrication) to minimize downtime. Don’t forget energy and dust considerations. By avoiding the pitfalls above and discussing the key questions with vendors, you can select a rip saw that boosts productivity, maintains quality, and operates safely and efficiently in your shop.