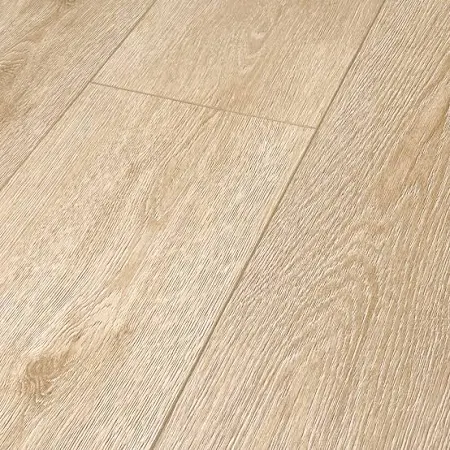
Wood Plank Multiple Blade Rip Saw Machine Drives Efficiency in Flooring Production
Wanhua Ecological Flooring, a mid-sized hardwood flooring and panel manufacturer, recently faced a bottleneck in its production line. Operating single-blade band saws, plant operators had to load and feed each plank by hand. This manual process was slow and labor-intensive, limiting daily output and leading to inconsistent board quality. Industry analysis of traditional monolithic saw systems notes that such setups tend to yield low production efficiency and require heavy manual labor, introducing safety hazards
To overcome these challenges, the company invested in a wood plank multiple blade rip saw machine production line. This state-of-the-art saw feeds planks on a conveyor track and simultaneously cuts each board with several circular blades in one pass. The production line features precisely machined blade spindle and automated controls. In practice, it can cut solid wood and engineered floor panels (such as laminate or composite flooring) into multiple strips of equal width in a single operation
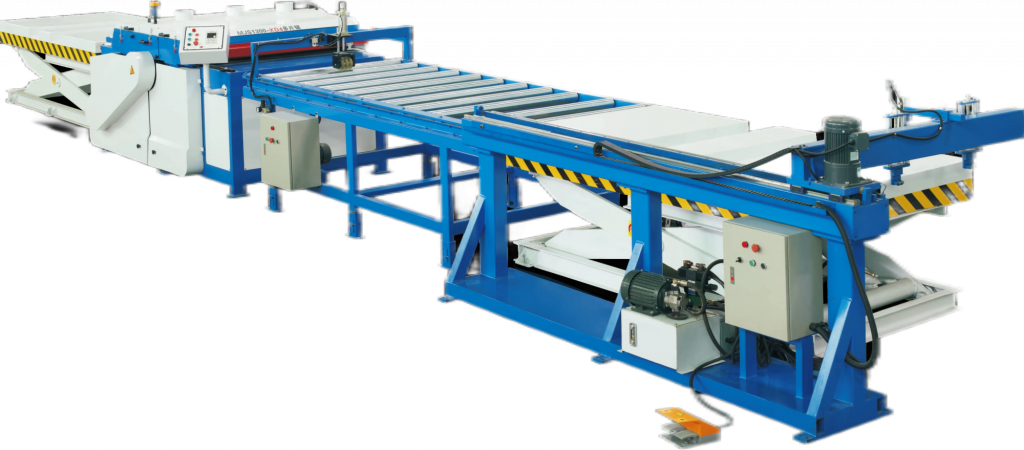
Challenges and Pain Points for Flooring Production
Before the upgrade, Wanhua Ecological Flooring’s production line suffered from several pain points:
- Low throughput: Cutting one plank at a time meant the old band saw could not keep pace with demand. As noted in equipment studies, traditional single-saw setups often have “low production efficiency” and limited capacity.
- High labor intensity: Manual loading and lengthy cuts required two or more operators per saw. Workers labored long hours to meet quotas, raising costs and introducing potential safety hazards.
- Inconsistent quality: Hand-fed cuts led to variations in board width and surface finish. Without automated sizing, extra milling and sanding were needed to achieve uniform flooring planks.
- Production bottlenecks: These issues together caused delays and inventory buildup, making it hard to satisfy large orders on time.
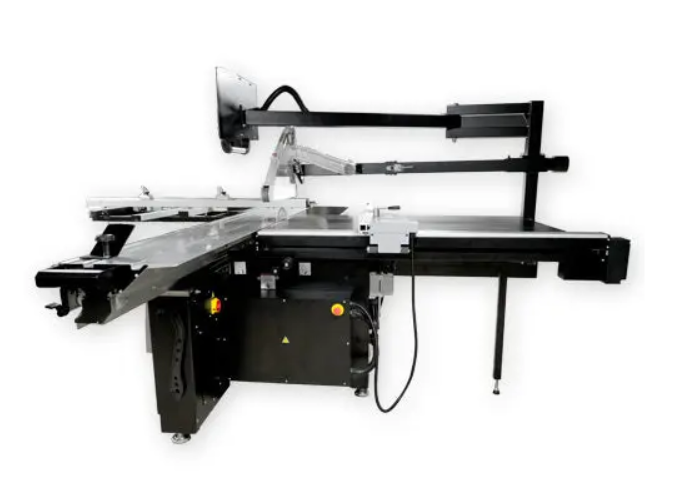
Selecting the Wood Plank Multiple Blade Rip Saw production Line
Wanhua Ecological Flooring’s engineering team evaluated several solutions and chose a robust wood plank multiple blade rip saw machine for their flooring line. Key considerations included reliable automation, precision cutting, and ease of operation. The selected production line offered these features:
- Automated feeding device: A motor-driven conveyor transports each plank steadily through the machine, eliminating manual pushing. There are multiple choices for automatic feeding, including gantry feeding, pushing feeding, suction feeding.
- Multi-blade configuration: Multiple saw blades are spaced across the width of the plank. In one pass, the machine cuts a board into several narrower strips.
- High-precision saw shafts: Heavy-duty spindles ensure each cut is straight and smooth. The manufacturer notes that the precision shafts guarantee the “smoothness and straightness” of every cutting plate.
- Enhanced safety: Enclosed covers and sensors reduce operator risk, enabling a safer, more ergonomic workflow. The patented anti-bounce device ensures the safety of the operation.
- Automatic end-product collecting: The hydraulic lifting table enables the automatic material collecting. Using the sensor to go up and down when material stacking. And manual removing by a forklift.
Together, these capabilities made the multi-blade rip saw production line an ideal choice for flooring production. The “high performance and high precision” design promised to dramatically speed up cutting while improving material utilization.
Implementation and Operation of Multiple Saw
Installation of the new rip saw went smoothly. Wanhua trained a small crew on the machine’s operation and safety procedures. Within days, operators were skilled at running full batches of plank cutting automatically. The hands-free feeding meant that one operator could oversee the process, whereas before at least two were needed per band saw. The line was reconfigured so that one multi-blade saw replaced multiple legacy band saws, freeing up floor space and labor.
As the production manager noted, “After the initial setup, running the multi-blade saw became straightforward. The changeover is fast and the machine runs continuously. It’s remarkably consistent compared to our old saws.”
Results: Efficiency and Quality Improvements
After deploying the wood plank multiple blade rip saw machine production line, Wanhua Flooring observed significant improvements:
- Higher Productivity: Production throughput increased dramatically. The factory could produce multiple times more board feet of flooring per shift. Overall output and material yield saw a major boost, aligning with findings that optimized multi-rip saws “greatly improve the wood yield and production efficiency”.
- Reduced Labor & Costs: Automation cut staffing needs in half. One operator now only need to inspect the machine for a while instead of two on manual saws. This not only lowered labor costs but also removed the manual feeding hazard, consistent with the device’s design goal of low labor intensity.
- Consistent Quality: Every board is cut to exact preset dimensions, eliminating the variability seen previously. The precision saw shafts deliver smooth, square edges, which reduced rework in finishing.
- Less Waste: Optimized cutting method minimized scrap. Offcuts were drastically reduced because the blade layout adjusted to cutting demand of the board width. This reflects the machine’s advertised benefit of “less waste, fewer processes, and higher profits”.
- Rapid ROI: The combined effect of higher output and lower overhead meant Wanhua recouped the machine cost quickly. As one manager put it, “We have effectively doubled our output and cut our scrap in half – the new saw paid for itself in just a few months.”
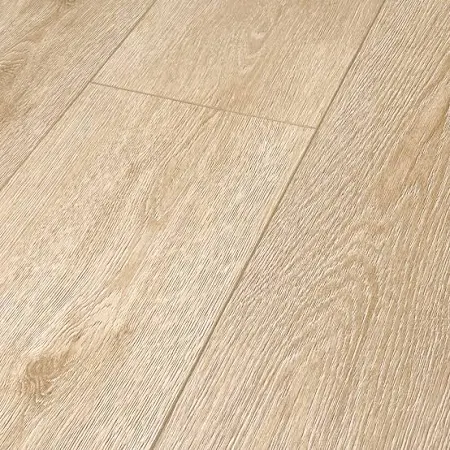
Wanhua Flooring’s success story demonstrates the powerful impact of a wood plank multiple blade rip saw machine on modern manufacturing. By addressing core production pain points – from throughput bottlenecks to labor costs – the multi-blade rip saw delivered measurable gains. The company achieved multi-fold increases in productivity, consistently precise cuts, and substantial savings. In summary, this case shows that investing in such advanced cutting technology can be a game-changer for manufacturers facing similar challenges.